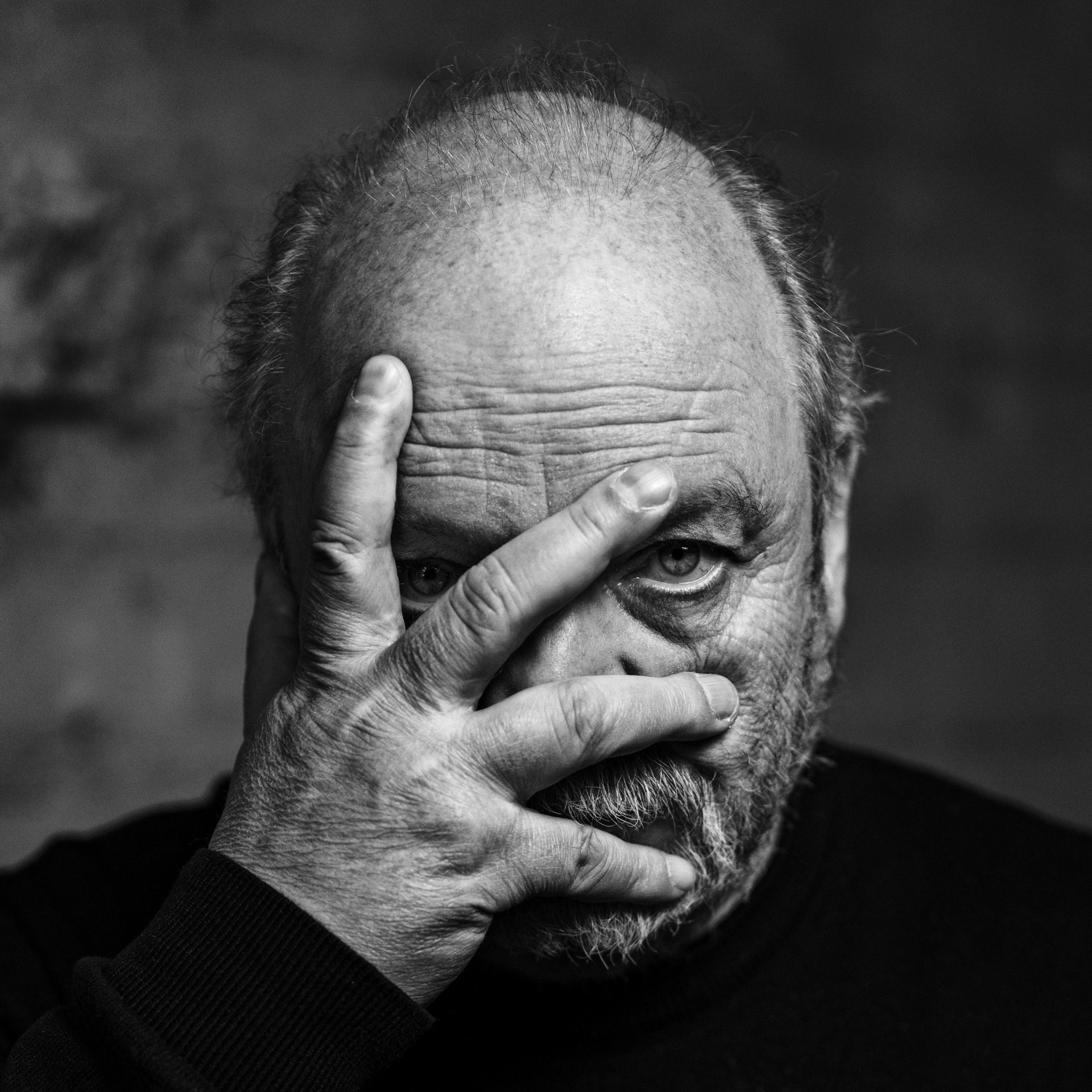
Inspired by his creative father-carpenter,
Peter Donders(°1965, Leut, Belgium)
studied furniture making at the well-known technical school in Maaseik.After graduating at the age of 22, he became a self-employed carpenter experimentingwith special shapes and materials
Driven by his continuous curiosity, Donders switched from pure craftsmanship to planning on the computer in 3D and CAD.
This self-initiated discovery marked a milestone in his career. Since that aha moment in 1999, he combines his experience as a craftsman with different computer-based tools in his artistic practice.
Ever since, Donders pushes the boundaries of existing technology and (crafting) techniques. He's always at the forefront of using the newest state-of-the-art technology,
integrating and translating it into fascinating artistic creations.
In doing so, he worked amongst others with carbon fiber, 3D printing and – his first love – wood.
Since2013, he also teaches 3D print product design at SYNTRA in Belgium.
Next to his autonomous work, he acts as a consultant in international teams designing some of the most impressive stadiums on earth.
In 2000 he designed the temporary construction of the theatre for the musical Grace in Amsterdam and in 2008, he designed the theatre seats for the Blackpools Grand Theater, pioneering in the combination of polygonal modelling and Rhino.
Since 2019, he cooperates with Seda Seating, working on projects in the United States, Canada and the United Kingdom.
From the Allegiant Stadium in Las Vegas (2019), the home of the Raiders football team, to the prestigious Madison Square Garden in New York City (2025).
An introduction to the milestones in his artistic work In his autonomous design and art, Peter Donders combines his background as a craftsman with his technological knowledge.
The computer is fully part of his production process allowing him to explore different materials and techniques.
Due to his fascination with the leading Belgian Art Nouveau architect Victor Horta, Donders' creations feature organic lines and serene shapes.
By combining contemporary technology, human wit and craftsmanship,
Donders manages to create surprising objects mimicking the natural world. They celebrate our human relation to nature.
For his C-bench and C-stone (2010) Peter Donders used carbon fibre,
for the processing of which he created an innovative technique. Because shaping asymmetric forms was so complex and an appropriate software did not exist yet, Donders decided to stick pieces of geodetic paths after each other. So, the fibre could later be assembled mechanically in one piece during production.
Although these organic forms without edges seem at first sight very simple, there is a lot of mathematics and calculation behind them. For a long time, Peter Donders was the only one in the world who could shape carbon fibre in such an organic way.
That's why the car, air and space industry worldwide showed much interested in his technique.
In Batoidea (2011), Donders experimented with a 3d printed sand mould, which is also used to produce the internal core of the Ferrari engine. The bright red colour is a wink to the famous sports car.
Moreover, the painting method and quality control are the same as in the iconic brand.
With his technical experience, Peter Donders stretches the possibilities of design.
The fluid and airy chair defies practical conventions. Aptly named for the genus of fish which includes the elegant stingray,
Batoidea is an extraordinary example of design and technology.
Morphsine,was his 1st sidetrack (2012-2013) 3d printed juwelery .
Solid Gold, Solid Silver and even Titanium,,,,,,
His next feat is the Ti-join chair (2015), which was part of the exhibition
'Making a difference/A difference in making. 25 years 3D printing by Materialise'.
The hybrid chair results from the assembly of 3D-printed metal joints and carbon fibre tubes.
Following principles of lightweight design, the joints provide rigidity and structural strength
with a minimal amount of material. So, 3D printing is applied where it can be of most service, helping to reduce production costs and indirectly benefit the environment.
In Shelly (2018) he fully integrates innovative techniques such as 3D-printing to transcend the purely artisanal.
The open, organic structure references to Art Nouveau. Based on a 3D print of the design, a mold has been made to cast the chair in bronze. At some points, you can still notice the original 3D print. Combining digital technology, artisanal knowledge and natural lines, the 37 kg bronze chair triggers the imagination.
With Dusty (2019), Peter Donders returned to his first love: wood. The chair is made from 3,5 sheets of 6-millimeter-thick Birch plywood plates. The original 3D model is cut into five parts, and each part is like a 3D print file sliced again. Each piece is numbered and positioned for 2D milling on a Zünd machine. Afterwards all 148 pieces are sorted and glued together into the five parts.
Everything is shaped by hand.
By combining crafts and computer technology, Donders managed to optimize the material use and its position to assure the strength and to decrease the weight to 5,9 kilos. In doing so, he realized a more cost-efficient and
shorter in production-time than on a traditional 5 axis milling. Moreover, less material is wasted. The organic shapes and plywood layers give the chair its exiting aesthetic and harmonious look.
For his tour-de-force Wind Bench (2020), Donders uses CNC robots to cut and slice his digital 3D model into plywood parts. After milling 210 slices of Birch plywood,
Donders sorts, glues, and shapes them by hand into 85 laminated layers. The final sanding and finishing achieve the bench's intricate, airy, streamlined appearance.
2nd sidetrack Digitwinss.com (2022) The Story of the MechEggs.
Digitwinss is a company that commercializes digital and physical products/Designs under license for the PeterDondersCollection.
The Spherene Sidetable (2024 in cooperation with 3D Systems )
is a fascinating example of how advanced 3D modeling and design software can optimize material usage while enhancing structural integrity. Using the Rhino3d plugin Spherene, designers can leverage advanced algorithms to reduce the amount of material needed without compromising, and often enhancing, strength. Here's some additional insight into how tools like Spherene can support this process and the benefits: